Finally got a chance to put the cyanotype UV boxes we worked on over the last couple of weeks into production! Max Mahoney (Chemistry), Christa Oberth (Chemistry), and Heike Schmid (Art) organized a Science Center activity working with students to produce cyanotypes. Following Max’s explanation of the process and the chemistry involved, and Heike’s discussion of the art history side of the equation, everyone got to work, some preparing paper by painting it with the sensitizer solution, others drying the still wet paper with a hairdryer, and others arranging materials and printing negatives.
Some students used feathers, leaves, and other object to create beautiful photograms, seen here through the UV filtering viewing panels Max and I built into the boxes…

…while others printed negatives on transparency film and used those to expose the photosensitive solution-treated paper.

A lot of folks showed up, so some used the exposure boxes, and others used good old fashioned sunlight to expose their prints.
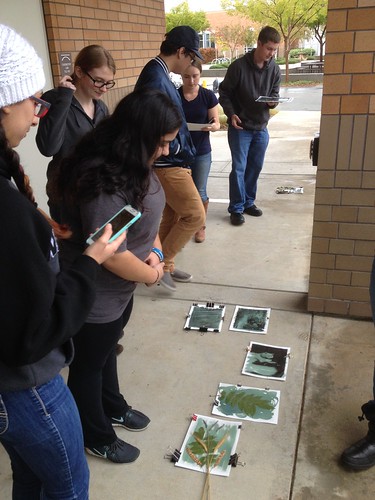
About 16 minutes in the boxes, or longer in the sun, and the prints were ready for a rinse, and some optional post-processing in a bath of hydrogen peroxide (which was supposed to enhance the prints, though students were divided on whether it really did much at all), or tea or coffee (for a sepia look).

I took the opportunity to reproduce a group photo from yesterday’s CCC Maker Advisory Committee.

Lots of ideas about how to improve the boxes – bigger, more LEDs, etc. – but very pleased with the version 1 results, and really pleased also to see faculty working on interdisciplinary projects!