Finally had the chance to set up the new Form 2 and give it a go. Met Max Mahoney (Chemistry) in the Innovation Center and we walked through the quick start guide.
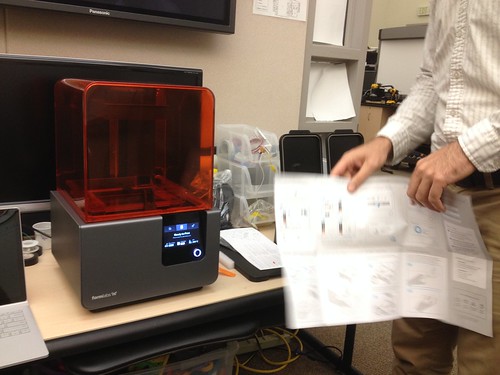
Once we got our head around the setup and leveling, we set up a print job. Originally, we planned to print Max’s molecule, but decided instead to try a set of some small parts from the OpenBCI headset. The software complained about some problems with the STL files, and then offered to automatically fix them, so we allowed it to.

The Form 2 has an interesting way of laying out objects, placing them all at a jaunty angle and adding a bunch of lattice-like scaffolding for support. There was a slight hiccup with the firmware update, but that was solved after a message to the Form 2 support folks. The solution was to download the new firmware and then select it, rather than letting the software automatically do that. Suggestion to FormLabs: Put a link to download the latest firmware on your support site, which would save calls/emails to support personnel.
Anyhow, the printer has a nice touchscreen interface, and navigating various functions is generally intuitive, though the network information – the printer can connect via Wi-Fi (admittedly in Beta) and Ethernet – is spotty and could use some work. Specifically, there don’t seem to be any diagnostics or deeper information about network connectivity, or a way really to know that the machine is able to get out to the Internet. In our college network environment, those kinds of diagnostic tools are crucial, as it is essentially a nightmare to get any device connected to the network. After connecting an Ethernet cable, the only information available was that the Form 2 received an IP lease. On the Wi-Fi side, I was not able to manually enter the name of the one hidden network available at the college that uses authentication simple enough to allow connection of strange devices. Finally, there doesn’t seem to be a way to trigger the leveling process except to wait for the machine to squawk about being out of level. It would be nice to be able to just trigger that process from the menu system. I hope those issues can be addressed at some point, but we were able to work around them and get the first print job uploaded.
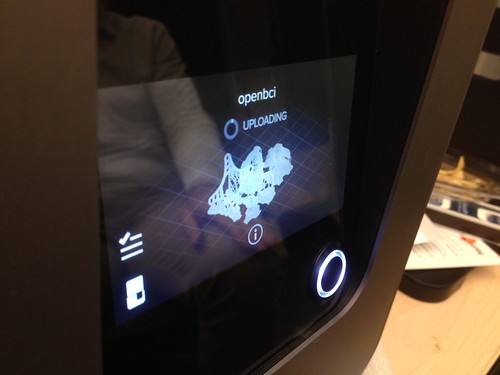
The printer ran the job, taking about 2.5 hours, and I streamed it live via the OpenBroadcaster setup. Post processing takes some getting used to, and involves nitrile gloves and bathing the parts in isopropyl alcohol at the finishing station. The print was a mixed success – some parts printed fine, and others were less than complete. My suspicion as that the “automatically fix the files?” part of the process didn’t actually work properly.
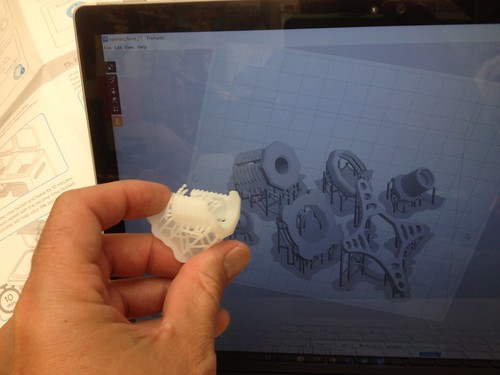
I do quite like that the printer sent me an email when the job was completed. My plan is to fix the files prior to importing them into PreForm, and then run the job again to try and get a better result. All in all, not bad for a first go, and we learned a lot about the process. Always be prototyping!